Investing in an automatic capsules filling machine is a critical step for any pharmaceutical, nutraceutical, or food supplement manufacturer. The right machine ensures high efficiency, accuracy, and compliance with regulatory standards. However, choosing the best one can be overwhelming due to the variety of models, specifications, and features available.
In this guide, we’ll cover everything you need to consider before purchasing an automatic capsules filling machine.
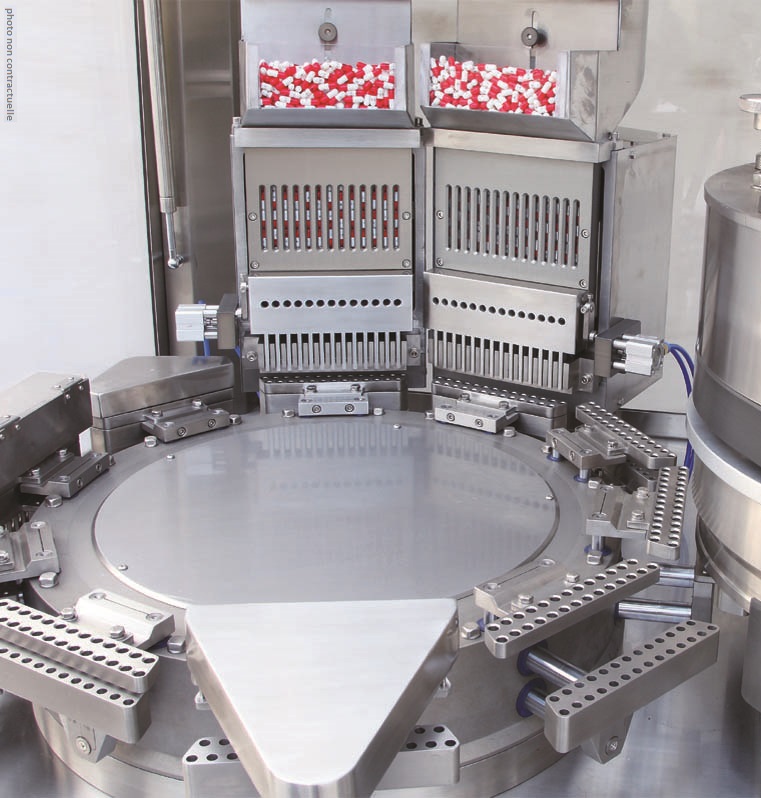
1️⃣ Understanding Automatic Capsules Filling Machines
What is an Automatic Capsules Filling Machine?
An automatic capsules filling machine is designed to precisely fill hard gelatin or HPMC capsules with different types of substances such as powders, granules, pellets, or even tablets. These machines play a vital role in large-scale production, ensuring speed, consistency, and quality control.
Main Components of an Automatic Capsules Filling Machine
✅ Capsule Hopper – Feeds empty capsules into the system
✅ Separation System – Separates capsule caps from bodies
✅ Filling Station – Doses the product into the capsules
✅ Closing System – Reattaches the capsule caps
✅ Ejection System – Collects the filled capsules for packaging
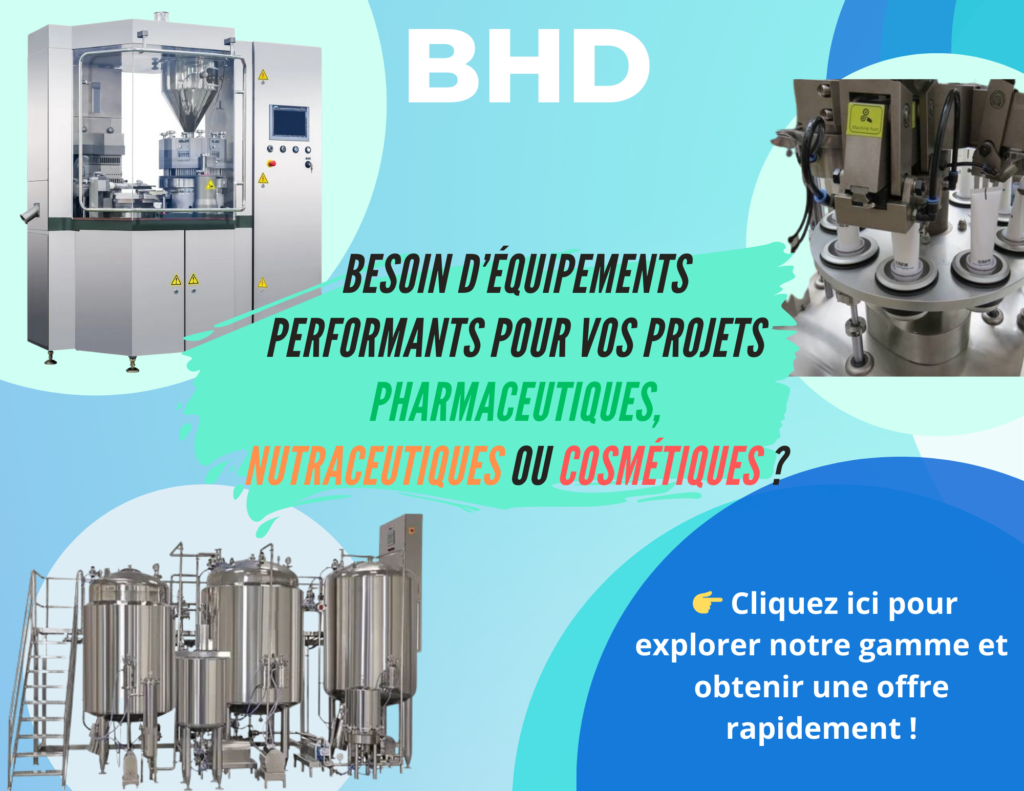
2️⃣ Key Factors to Consider Before Buying
1. Type of Product to Fill
Before selecting a machine, determine the form of the product you will be encapsulating:
✔ Powders – The most common form, requiring a tamping or dosator filling system
✔ Granules & Pellets – Used for controlled-release formulations
✔ Tablets or Mini-Tablets – Requires special configurations
✔ Liquid – Requires a specific liquid-filling system
2. Production Capacity
Choose a machine based on your required output capacity:
🔹 Small-Scale Production: 5,000 – 25,000 capsules/hour
🔹 Medium-Scale Production: 25,000 – 100,000 capsules/hour
🔹 Large-Scale Production: 100,000+ capsules/hour
3. Capsule Sizes Compatibility
Ensure that the machine can handle the capsule sizes you need (from size 000 to size 5). If multiple sizes are required, change parts must be ordered accordingly.
4. Machine Automation Level
There are three levels of capsule filling machines:
✔ Manual – Labor-intensive, suitable for small batches
✔ Semi-Automatic – Requires some manual intervention but offers higher output
✔ Fully Automatic – Best for large-scale production, minimal human intervention
5. Change Parts Availability
Since different formulations and capsule sizes require different filling mechanisms, ordering change parts is crucial to maintaining machine versatility.
6. Regulatory Compliance
Ensure the machine complies with cGMP, FDA, and EU regulations, including:
✅ Use of stainless steel (SS 316L) for contact parts
✅ Dust collection and air filtration systems to prevent contamination
✅ Compliance with 21 CFR Part 11 if electronic data recording is needed
7. Integration with Other Equipment
Consider whether the machine should integrate with:
🔗 Blistering machines – For direct packaging
🔗 Powder blenders – To mix ingredients before encapsulation
🔗 Capsule polishing and sorting machines – To ensure finished capsules are free of defects
3️⃣ Top Features to Look for
💡 High Filling Accuracy – Reduces material wastage
💡 Easy Cleaning & Maintenance – Tool-free disassembly for faster changeover
💡 Smart HMI Control Panel – Touchscreen with programmable settings
💡 Built-in Sensors & Alarms – Detects capsule defects and product misalignment
💡 Flexible Dosing System – Ability to fill different product types
4️⃣Final Checklist Before Purchase of an Automatic Capsules Filling Machine
✅ Does the machine match your production needs?
✅ Can it fill the right type of product (powder, pellets, granules, etc.)?
✅ Is it compatible with the capsule sizes you need?
✅ Does it meet GMP and regulatory requirements?
✅ Are change parts available for different formulations?
✅ Can it integrate with other production line equipment?
Choosing the right automatic capsules filling machine is essential for ensuring efficient, high-quality pharmaceutical or nutraceutical production. By evaluating your product type, capacity needs, compliance requirements, and integration possibilities, you can make an informed purchase decision that will optimize your production efficiency.
Retrouvez plus d’articles sur https://bhd.ma